Customer Story
Takeda improves human performance with DevonWay software
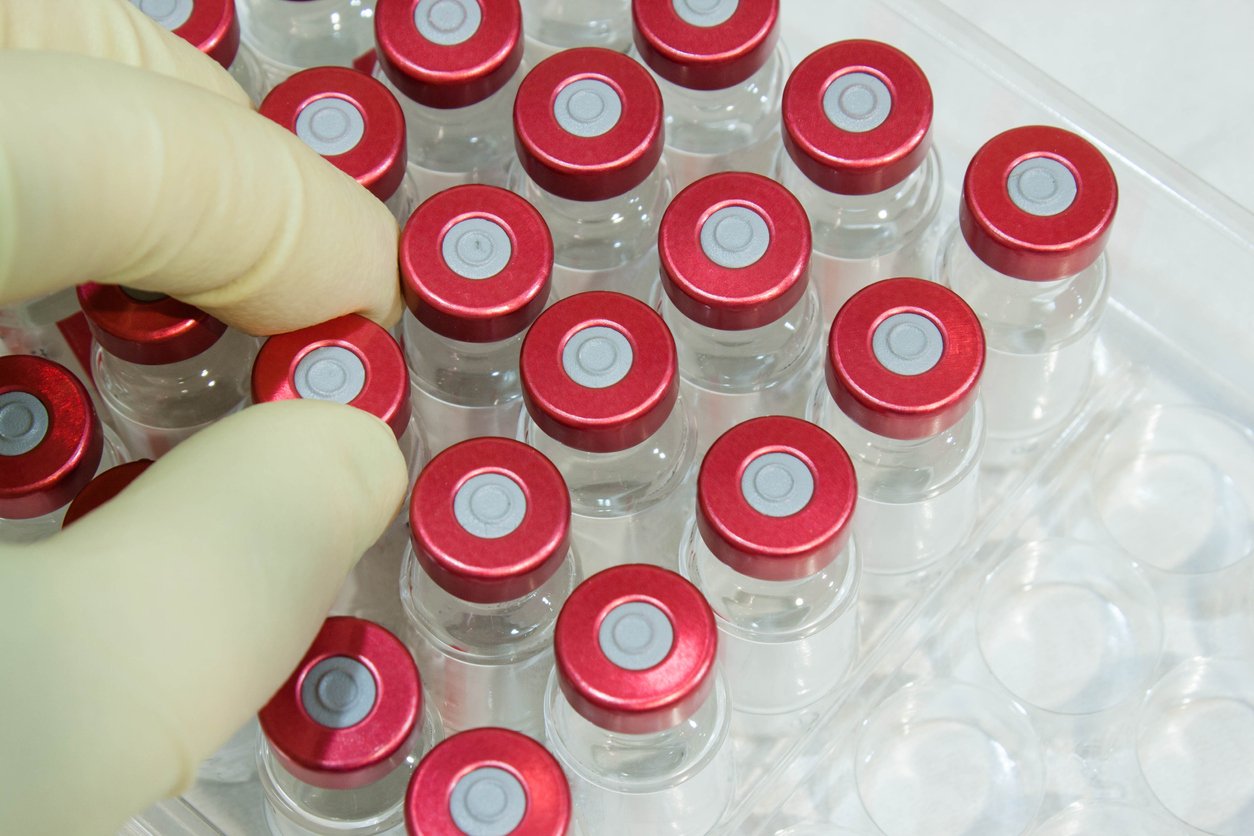
Creating more success through human performance at Takeda
Takeda’s Massachusetts Biologics Operations site implemented DevonWay Observations, internally called Operational Learning Gemba, and DevonWay General Actions, as part of their Human & Organizational Performance road map.
The percent of manufactured batches that are manufactured successfully the first time (aka Batch Right The First Time) is an important measure of quality in biotech: The higher it is, the lower the waste and loss in the manufacturing process. Along with other efforts at the site, the DevonWay solution contributed to a 20% improvement in Batch Right The First Time.
Reducing Human Performance Risk to Increase Yields
We spoke with Clifford (Cliff) Berry, Head of Business Excellence at Takeda’s Massachusetts Biologics Operations site. He’s been a Human and Organizational Performance practitioner since 1999 and has experience in biopharma, commercial nuclear electrical generation, electric transmission and distribution, and the US Navy.
What is Human Performance – and Why Is It Important?
“In biotech it basically means protecting people and products from harm,” Cliff told us. In pharmaceutical manufacturing, product harm includes issues like product contamination, quality departures, losing data, and even sending the contents of a vessel to a place that it is not intended to go – the drain or the floor.
One definition for Human Performance, or Human & Organizational Performance, is understanding how people interact with plant, processes, and each other – as part of a system, to manage risk to protect people and product from harm by establishing necessary capacities and controls.
“Human Performance as a name can be misleading,” laughed Cliff, “because we are improving systems, not fixing people.” In biotech manufacturing, Human Performance is about managing operational risk and failure. It combines domains that include systems safety, human factors, safety science, and resilience engineering.
Software for Human Performance
When Cliff joined Takeda Massachusetts, the team wrote observations on paper cards, which was time consuming and didn’t provide much-needed visibility. To encourage participation, gain visibility, and improve quality, he knew they needed easy-to-use software to automate observations and follow-up actions.
Cliff reviewed the site’s existing audits and assessments software and realized that it would not work very well for Human Performance. The legacy system was rigid and nonintuitive. Its workflow capabilities weren’t flexible. More importantly, it used terminology that discouraged a Human Performance mindset. Human Performance recognizes that the worker is the solution to the problem, not the problem, so the approach and language are different from traditional inspections, audits, assessments, and corrective and preventive actions programs.
The team needed flexible software that:
- Enables quick changes to fields, pick lists, and workflows to fit their Human Performance program goals and can reflect colleagues’ requests for changes.
- Engages the workforce with easy-to-use interfaces on desktop and mobile.
- Has flexible, configurable workflow options, enabling colleagues to choose who (individuals or teams) needs to do what when.
- Includes business intelligence, trending, and reporting functionality that business users can use without involving IT.
- Provides robust action tracking and configurable notifications to ensure follow-up and support learning.
The DevonWay Human Performance Solution
Cliff turned to DevonWay, a vendor he’d worked with successfully at a prior company. “I know of other vendors that once you’ve paid them, you’re stuck on an island, and they don’t help you. Not with DevonWay – when we need changes, we get fast turnaround.” He often makes changes himself in response to his users’ feedback.
Internally, Takeda calls its observation solution Operational Learning Gemba, because gemba is a common term in manufacturing operations where Lean Six Sigma is used. (“Gemba” is Japanese for “the real place,” now adapted in management terminology to mean the 'workplace' or the place where value is added.)
Leaders enter Observations and optionally add follow-up Actions. Actions are assigned, reviewed, and tracked to completion.
Users are automatically notified when Actions assigned to them are coming due or overdue. The system distributes weekly management reports by email to the site leadership team and manufacturing managers, who can view the summary information within the email or click to open the record in a browser for more details.
Results: Increased Learning, Improved Outcomes, Cost Savings
With the DevonWay system, the site leadership team now has visibility into engagement and progress. Cliff tracks time and resources invested in operational learning.
Along with other efforts at the site, the DevonWay solution helped improve Batch Right The First Time by 20%. As deviations that contribute to Batch Right The First Time are addressed through systems improvements, the likelihood of no batches being lost is improved. In pharmaceutical manufacturing, a batch loss can cost $2 million or more, so improvements quickly add up to many millions of dollars saved.
“Two key elements of a Human Performance program are learning and fixing,” Cliff says. “You have to watch work and engage with the experts who perform the work, and Operational Learning Gemba helps our leaders to learn about work in a very effective manner.”
Learn more
For guidance on the discipline of Human Performance in pharmaceutical operations, see Human Performance in Biopharma Operations – Your Problem Isn’t Error (November 9, 2020) and Moving Beyond Human Error In Biopharma Investigations and CAPA Programs (November 16, 2020) in Pharmaceutical Online.
Click here for more info on DevonWay solutions for biotech and pharmaceutical manufacturing.
Story Snapshot
Challenges
Takeda needed easy-to-use human performance software to support their Human & Operational Performance road map at the Massachusetts Biologics Operations site.
Solution
DevonWay Observations powers Takeda's Operational Learning Gemba. Leaders enter human performance observations and optionally add follow-up actions. The site leadership team and managers have visibility into engagement and progress.
Results
Along with other efforts at the site, the DevonWay solution helped improve Batch Right The First Time by 20%. A batch loss can cost $2 million or more, so improvements quickly add up to many millions of dollars saved.
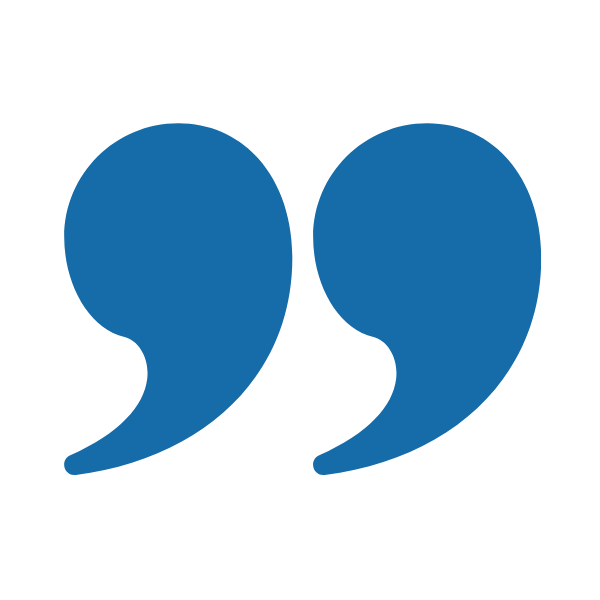
It's been an excellent experience with Devonway. We need to track multi-million $ productivity improvement projects across the globe and Devonway has made that seamless.
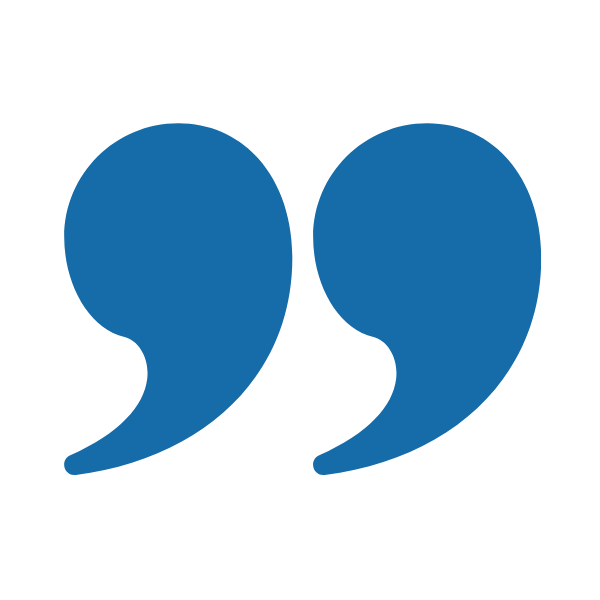
I know of other vendors that once you’ve paid them, you’re stuck on an island and they don’t help you. Not with DevonWay – when we need changes, we get fast turnaround.
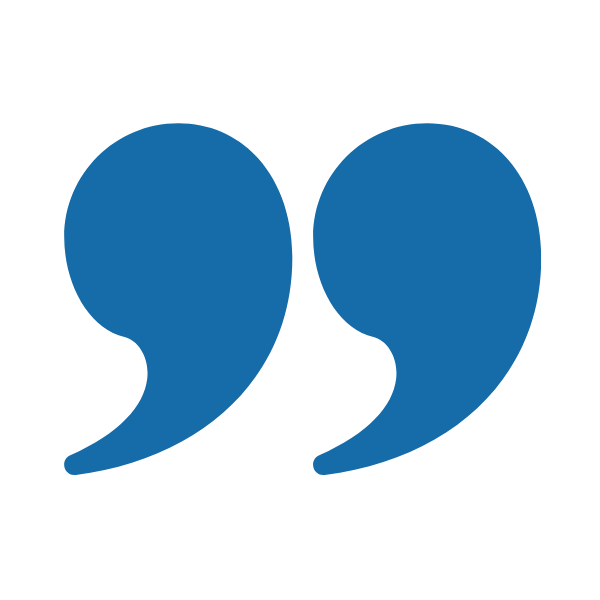
I use the relationship we have with DevonWay as our gold standard when we work with outside entities. I don’t know anyone I work with outside of NPPD that we have such a good relationship with.